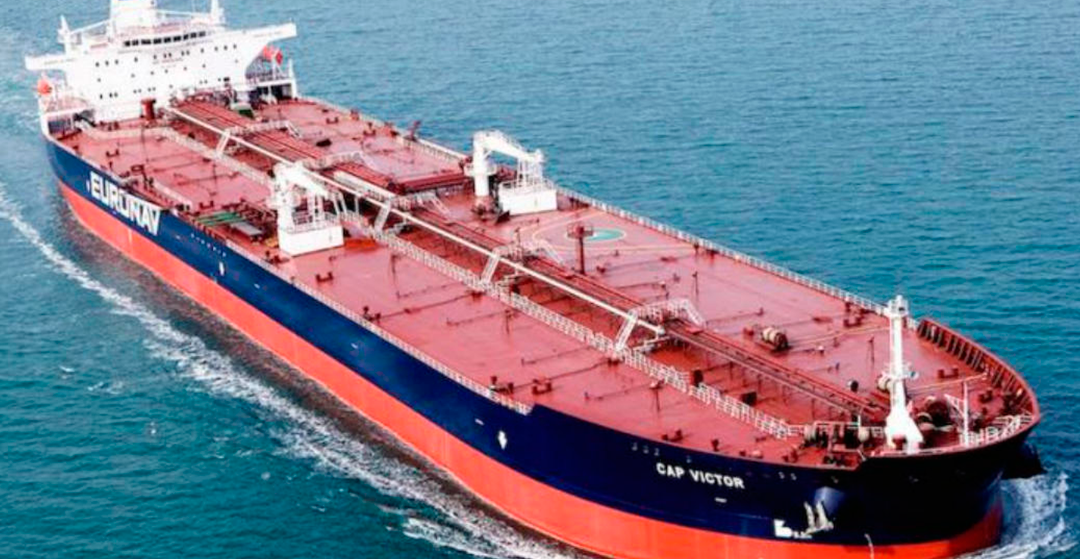
In the following article we would like to share with you some basic concepts about the cleaning tasks and techniques in petrol vessel tanks. Those cleaning processes depend on the situation, and therefore the decision of which products to apply must be taken by the people responsible for the cleaning.
Purgat Química has two great products available to clean tanks of fuels located both in land and in oil tankers.
Our new and powerful detergent BTI-BIO (SEE PRODUCT) is produced specifically for this purpose following the protocol MARPOL3 and it is homologated by the General Director of the Mercantile Marine.
This amazing product can completely clean surfaces and remove any residue and sediment that might show up during the cleaning process.
Another product we offer for hard cleanings in oil tankers is VERQUIM-2 (SEE PRODUCT) which is indicated to apply in areas and surfaces that have been affected by specific dirt from mineral oils, hydrocarbons, greases, etc.
CLEANING TASKS
Cleaning tasks of tanks with sea water are carried out for several reasons:
- Maintenance tasks (repair, sediment accumulation or inspections) which require to enter the tank.
- Change the grade of the product.
- Requirements of the charterer.
- Clean ballast
- Entering a dry dam
- Due to regulatory requirements
Cleaning processes were originally carried out with hand-held hoes. Once the tank had been degassed, the operators would enter the tank with the hoes.
This was a dangerous, expensive, and highly inefficient process, since it could not achieve an adequate cleaning.
As the size of ships increased, the manual cleaning system required had to be improved. Mechanic cleaning systems were introduced to ensure an adequate cleaning of ships.
EFFICACY OF THE CLEANING
The efficacy of the cleaning depends on the following parameters:
- Amount of fluid discharged
- Discharge pressure
- Rotatory speed of the machine
- Precision in which it can cover the surface of the tank
Those cleaning systems can be divided in:
1. Mobile cleaning machines
2. Fixed cleaning machines
In the following article we will explain in-depth the characteristics and properties of those cleaning systems.
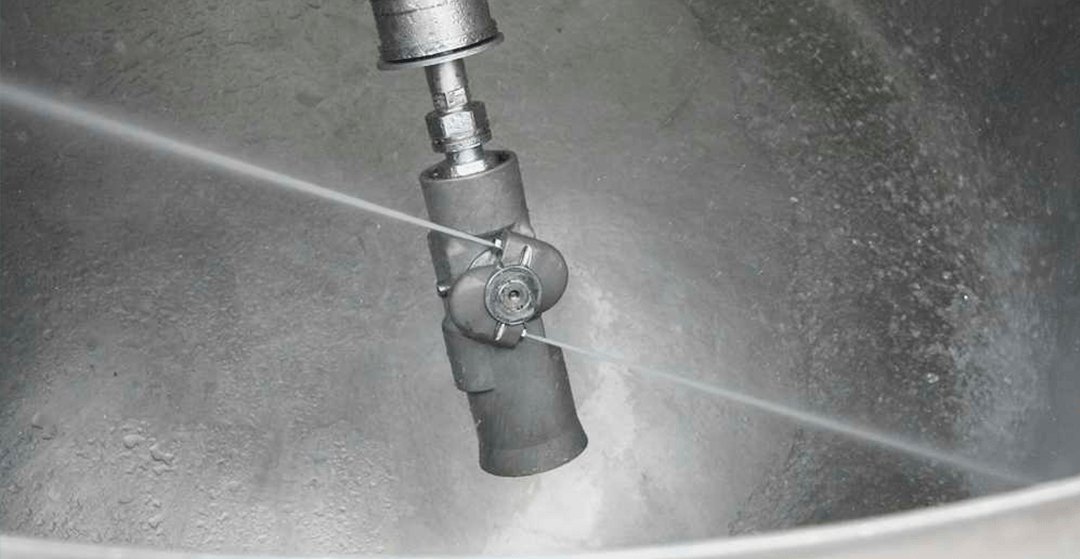
CLEANING TECHNIQUES
Throughout the entire cleaning process the main objective is the total cleaning of the tank, for this reason it is important to consider that both the cleaning techniques and the product used will affect the result.
Cleaning techniques can be distinguished between cleaning in a single stage and cleaning in two or more stages.
Cleaning in a single stage:
This process consists in cleaning the tank entirely without interruptions until it is fully cleaned.
In order to carry out this cleaning process, the tank must be dry, and therefore there must be no accumulated liquids in the place throughout the cleaning process.
Cleaning in two stages:
This process consists in dividing the entire cleaning of 280º in two phases, one for each plane, the upper plane and the lower plane.
It is recommended that this cleaning process is done with programmable machines in order to minimize the costs by cleaning only the areas that we wish to clean.
In the single-stage cleaning, we had a machine that carried out a continuous cleaning of the tank without interruptions in a range of 280º. In this case, the cleaning is divided in two stages, in which each stage is a plane, the lower plane and the upper place.
Upper plane
The upper plane is cleaned with a cleaning program with an angle of 140º – 50º in the vertical axis and with 360º of
Lower plane
The lower plane is cleaned with a cleaning program with an angle of 50º – 0º – 50º in the vertical axis and with 360º of horizontal axis of rotation.
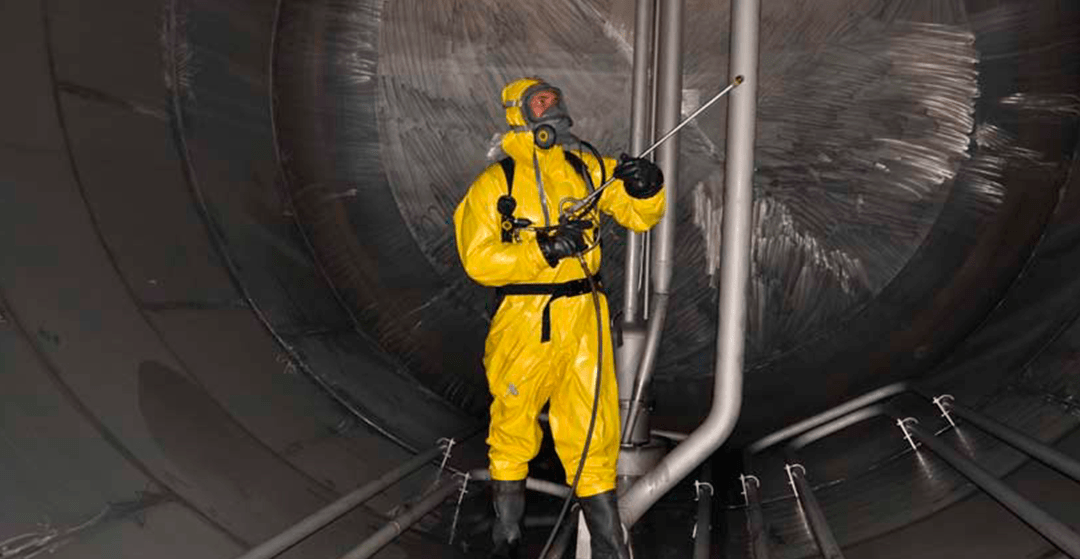
Process:
Approximately 3/4 of the content of the tank is poured, around 3 meters of sonar.
Then we proceed to clean the upper plane (roof) and the sides of the tank.
As we undertake the cleaning process, we continue with the discharge until it is ready to dry with the ejectors.
Once the tank is dry, we clean the lower place and the side of the tank which was not previously cleaned.
Observations
During the discharge both techniques are combined if the cleaning is done in several tanks at the same time in order to spend less time with the cleaning process.
Regarding the programming of the machines, you must take into account the configuration of the tank you want to clean. For example, a central tank in an oil tanker has smooth bulkheads, which makes it harder to clean the lower plane, while the lateral tanks have longitudinal reinforcements in the vertical sides, and therefore a large quantity of sediments are accumulated there.